Aufbruch in eine sichere Zukunft
Es war das erste Mal in der Historie der Karosseriefertigung, dass derart geometrisch hoch komplexe und ultra-hochfeste Komponenten mit Hilfe des Presshärtens in industrieller Großserienfertigung hergestellt und in den Fahrzeugen verbaut wurden.
2004: Start der Serienfertigung für die Komponenten des ersten ultrahochfesten „Sicherheitskäfig“-Designs für die Fahrgastzelle des Volkswagen „Passat“. Erfolgreiche Implementierung des Presshärtens in die Großserienfertigung im Volkswagenwerk Kassel. Nr 1 © Christina Czybik/VWPics / Alamy Stock Foto Nr 2 © Christina Czybik/VWPics / Alamy Stock Foto Nr 6 © METAKUS / Foto: Mario Zgoll
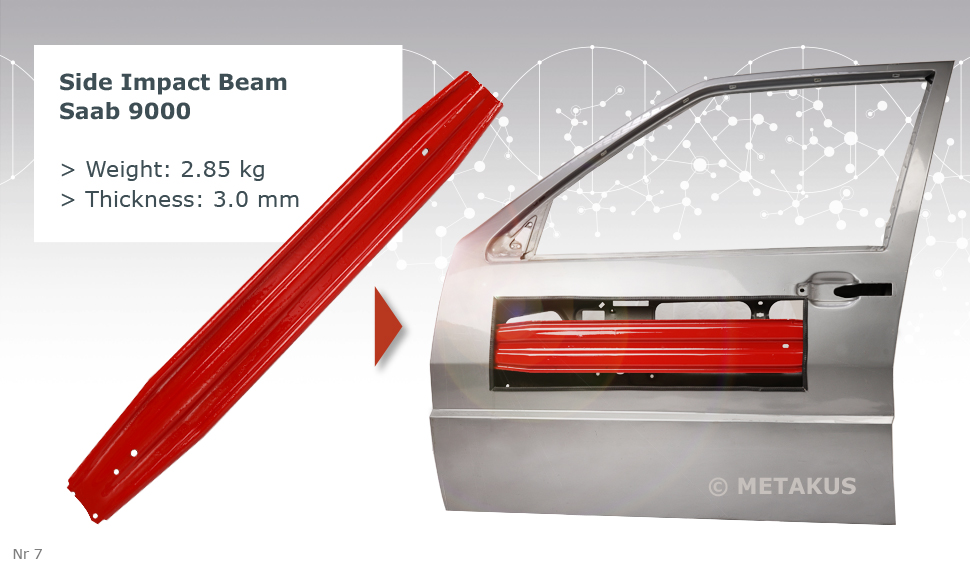
SICHERHEIT VON ANFANG AN
Dabei war die Technologie des Presshärtens im Grunde seit Anfang der 70er Jahre des letzten Jahrhunderts bekannt. Pressgehärtete Strukturkomponenten wurden seit Mitte der 80er Jahre erstmalig im Karosseriebau eingesetzt. Zu diesem Zeitpunkt ging es jedoch einzig und allein darum, eine Lösung für die gestiegenen Sicherheitsanforderungen für die Fahrzeuginsassen zu finden. Ergebnis waren einfache, profilähnliche Verstärkungskomponenten, die vorwiegend zur Erhöhung der Intrusionssicherheit im Falle des Seitenaufpralls in den Fahrzeugtüren verbaut wurden. Diese Komponenten waren allerdings alles andere als leicht.
STAHL, ALLES ANDERE ALS EIN SCHWERGEWICHT
Mit dem seit den 90er Jahren dramatisch gewachsenen Bewusstsein, dass Umwelt- und Klimaschutz auch und vor allem einschneidende Maßnahmen im Bereich des Individualtransportes verlangen, wurden Forderungen nach einem effektiven Leichtbau für Personenfahrzeuge zunehmend lauter.
Dass der Werkstoff Stahl aufgrund seines wirtschaftlichen und technischen Potenzials dabei nach wie vor eine gewichtige, allerdings deutlich gewichtsreduzierte Rolle spielen sollte, erschien unumgänglich.
Zentrales Kriterium für den Leichtbau war und ist nach wie vor dabei eine möglichst hohe intrinsische Belastbarkeit durch die Einstellung höchster Werkstofffestigkeiten.
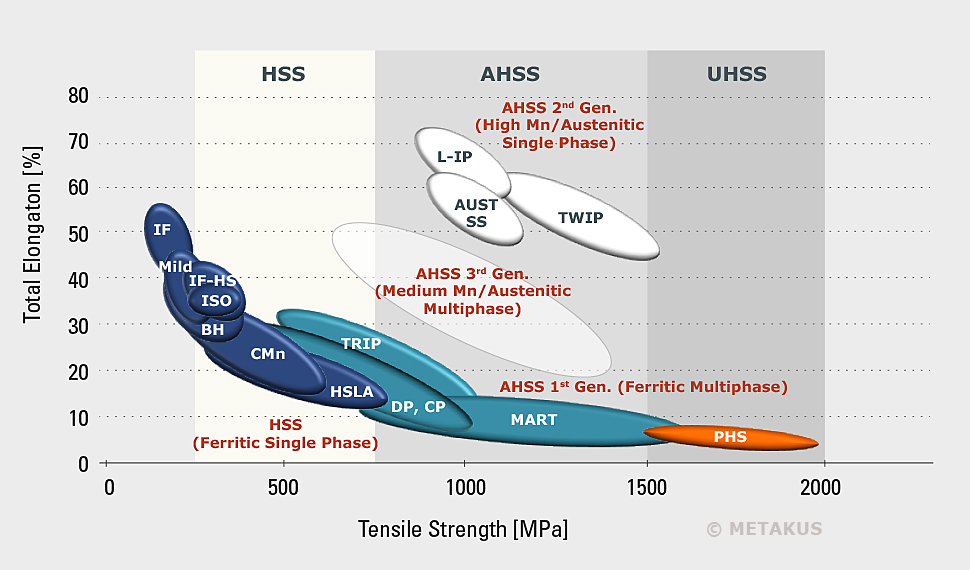

WÄRME, DER SCHLÜSSEL ZU HÖCHSTEN FESTIGKEITEN
Bewegt man sich allerdings zu derart hohen Festigkeiten, dann grenzt sich die Auswahl verfügbarer Stähle auf solche Güten ein, die ihre Eigenschaften erst durch eine gezielte Wärmebehandlung entfalten.
Genau diese Gruppe von Stählen adressiert das Presshärten. Dabei ist es die Besonderheit, dass durch Einbettung der Formgebung in den Temperatur-Zeit-Zyklus des Härtens nicht nur die erwarteten höchsten Festigkeiten erreicht werden, sondern auch überaus komplexe Bauteilgeometrieen mit vergleichsweise geringen Formgebungskräften in einem einzigen Prozessschritt eingestellt werden können.
Mit den in der Fahrgastzelle des Passat ab 2004 in Serie verbauten pressgehärteten Komponenten wurde eine bisher nie dagewesene Leichtbaudimension gepaart mit höchster Sicherheit erreicht.
MEILENSTEIN IM AUTOMOBILEN LEICHTBAU
Für Professor Weißner besteht kein Zweifel: Die erfolgreiche Implementierung des Presshärtens in der Großserienfertigung bei der Volkswagen AG wäre ohne die maßgebliche Wegbereitung und Unterstützung durch Professor Steinhoff und seinem Team undenkbar gewesen. Rückblickend stellt dies einen Meilenstein für die zukünftige Gestaltung und Herstellung von Leichtbaustrukturkomponenten für den Automobilbau dar.
Die Keimzelle der heutigen METAKUS Automotive wurde dabei 2007 bereits mit der Grundsteinlegung des gleichnamigen Technologiezentrums in Kassel gelegt. Dessen Geschäftsführer war über lange Jahre nach Eintritt in seinen Ruhestand Professor Weißner. Über weit mehr als ein Jahrzehnt wurden hier die wesentlichen Bausteine des genetischen Codes des Presshärtens unter der wissenschaftlichen Leitung von Professor Steinhoff geprägt.
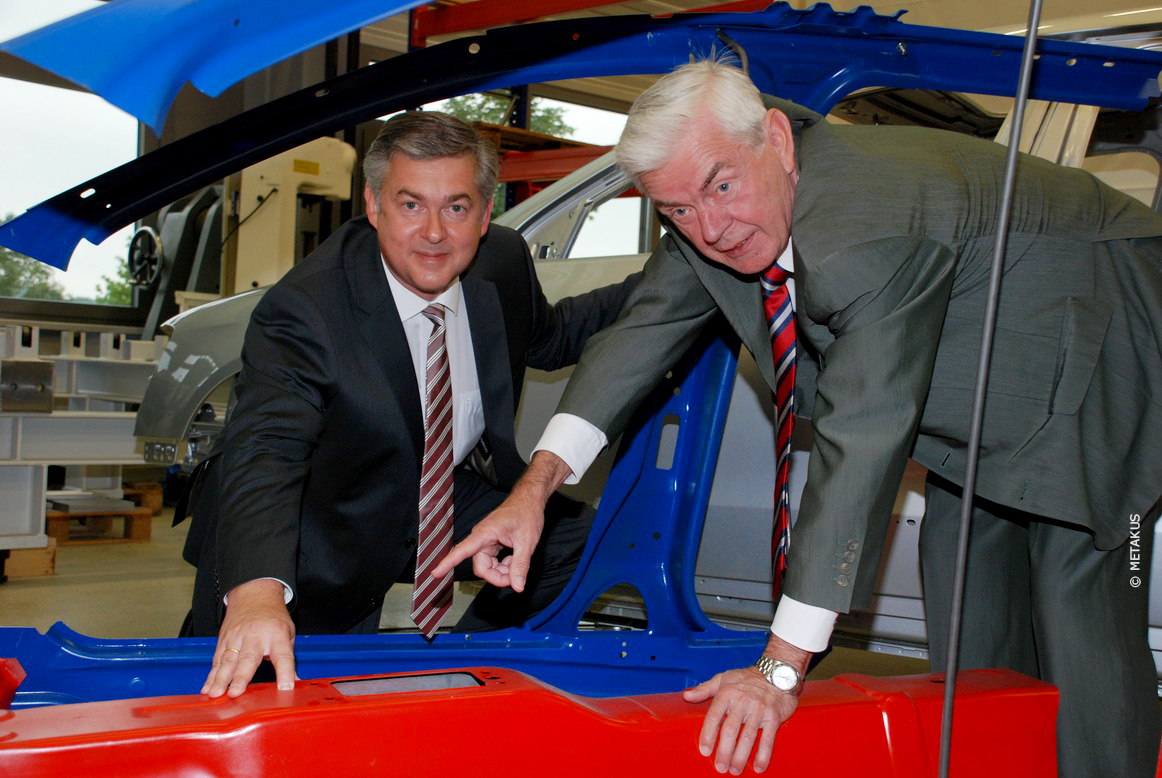