FUNCTIONAL GRADATION – FROM THE DREAM TO REALITY
The realization that integral component properties must always be oriented in accordance with the highest load, but that they are frequently only appear in locally restricted component areas was reached many years ago, and resulted in the idea to implement graded properties, meaning properties actually oriented in accordance with the actual load profile.

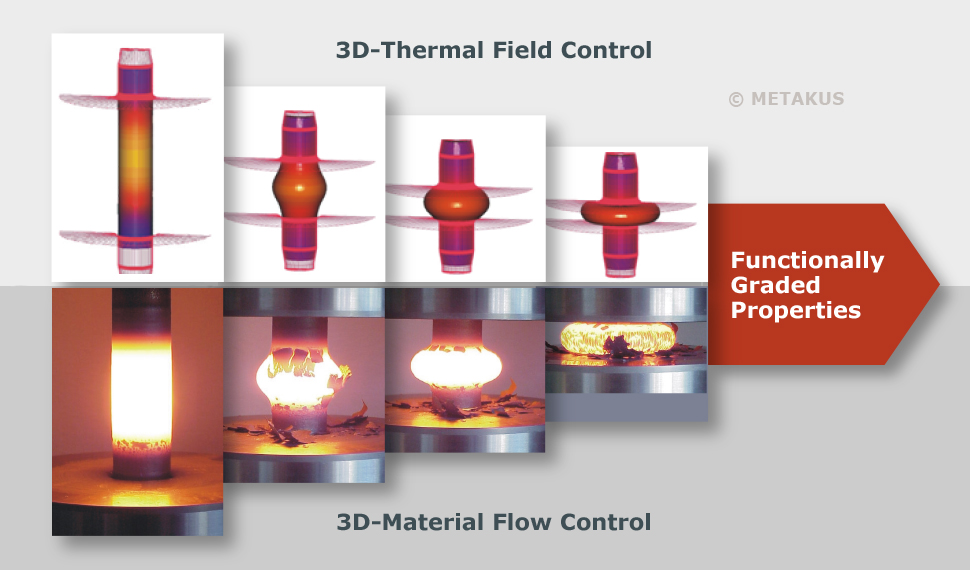
TAILORED FOR FUTURE CHALLENGES
For a very long time, the decisive transition into industrial mass production was missing. Based on his first developments in the mid-90s, Professor Steinhoff illustrated how such an approach can be applied to monolithic workpieces made of traditional construction materials if synchronization of the geometric complexity with an equally complex distribution of material properties is achieved in a single component by means of the processing technique.
His solution approach involving metal forming processes with locally and temporally variable temperature control was groundbreaking for the industrial mass production of functionally graded components.
GETTING STARTED IN LIGHTWEIGHT AUTOMOBILE CONSTRUCTION
After press hardening in the core area of the car body that comprises highly sensitive safety aspects was able to be established based on his substantiated findings, Professor Steinhoff was very interested in using his findings for property gradation that had been tested for years to develop a solution approach for effective lightweight construction on the one hand, and frequently opposing requests for multifaceted crash management on the other.
When the coupling area of the lower B pillar section that connects to the floor assembly threatened to develop into an increasingly critical issue due to the incompatibility of the achievable ultra-high strengths in press hardening and the ductility required for energy absorption here, the solution was evident.
The adjustment of thermomechanically tailored property distribution as an integral part of press hardening.
Transmission of kinetic energy during side impact by means of controlled plastic deformation of the soft lower B pillar section into the floor assembly of the vehicle. Nr 9 © 3DMI/Shutterstock.com; Montage METAKUS Nr 10 © 3DMI/Shutterstock.com; Montage METAKUS Nr 11 & 12 © Insurance Institute for Highway Safety, Arlington, Virginia USA | www.iihs.org
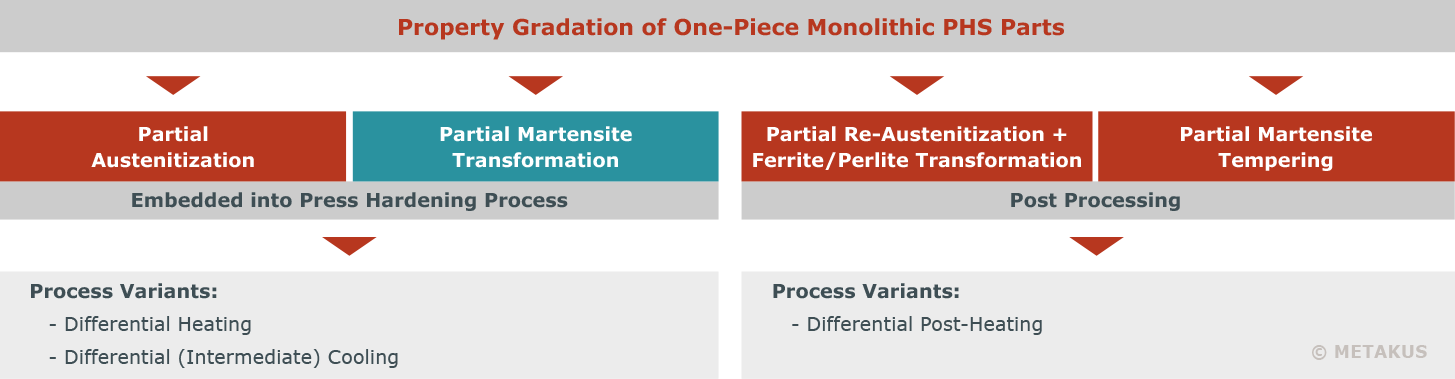
2006: SOP of first thermomechanically tailored component in large series automotive production. High ductility of the lower B pillar section enables energy absorption, ultra-high strength of the center, and the upper section offers sufficient intrusion resistance and roll-over stability. Nr 3 © imageBROKER / Alamy Stock Foto; Montage © METAKUS Nr 4 © CoverSpot Photography / Alamy Stock Foto; Montage © METAKUS
A GLOBAL SUCCESS STORY
More than two decades after the first idea, the novel design approach developed into a global megatrend for automobile construction beginning in the 2000s with the manufacture of ultralight and simultaneously extremely safe car body components.
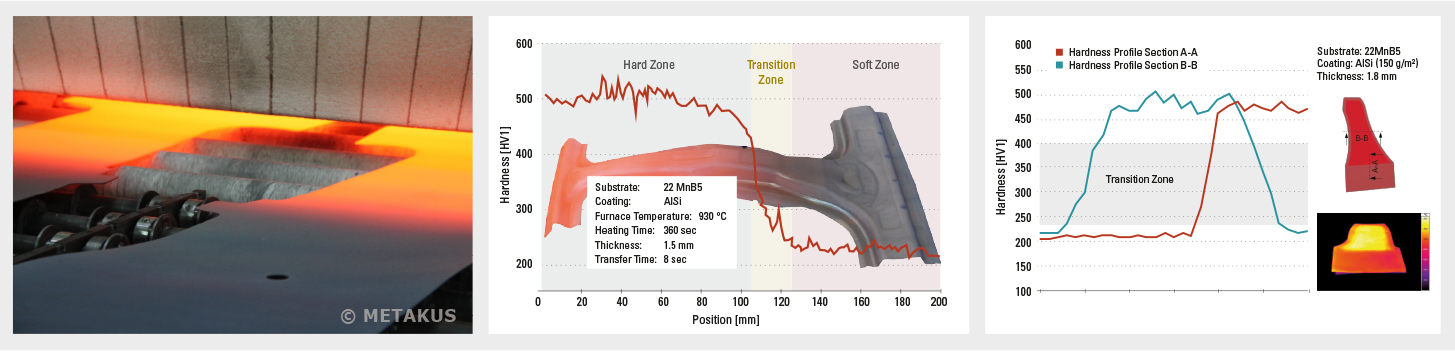
2006: Differential intermediate cooling during press hardening of a B pillar reinforcement as first applied in large series production of functionally graded car body components. (left) 2004: Characteristic hardness profile of a B pillar reinforcement after press hardening in a tool running on locally and temporally variable thermal conditions - differential in-die cooling. (middle) 2011: Hardness profiles and thermographically measured temperature distribution of a B pillar reinforcement with tailored heating. Complex soft-zone and soft-flange pattern produced by differential intermediate cooling. (right)
AT THE INTERSECTION BETWEEN RESEARCH AND PRACTICE
Owing to this groundbreaking idea and the unique expertise of Professor Steinhoff and his team, a world-class technological hotspot for press hardening was developed at the University of Kassel in 2005 with the initial establishment of the application center METAKUS. Countless impulses began there and essential developments were made market-ready there for their move into industrial series manufacture. METAKUS is the training ground for numerous experts in press hardening technology.
These priceless resources represent the “genetic code” of METAKUS Automotive with their extensive performance profile in the field of press hardening technology. After more than two decades, Professor Steinhoff is still the mentor, but a number of certified experts ensure continuity and performance capacity that seek their equal on the international level.
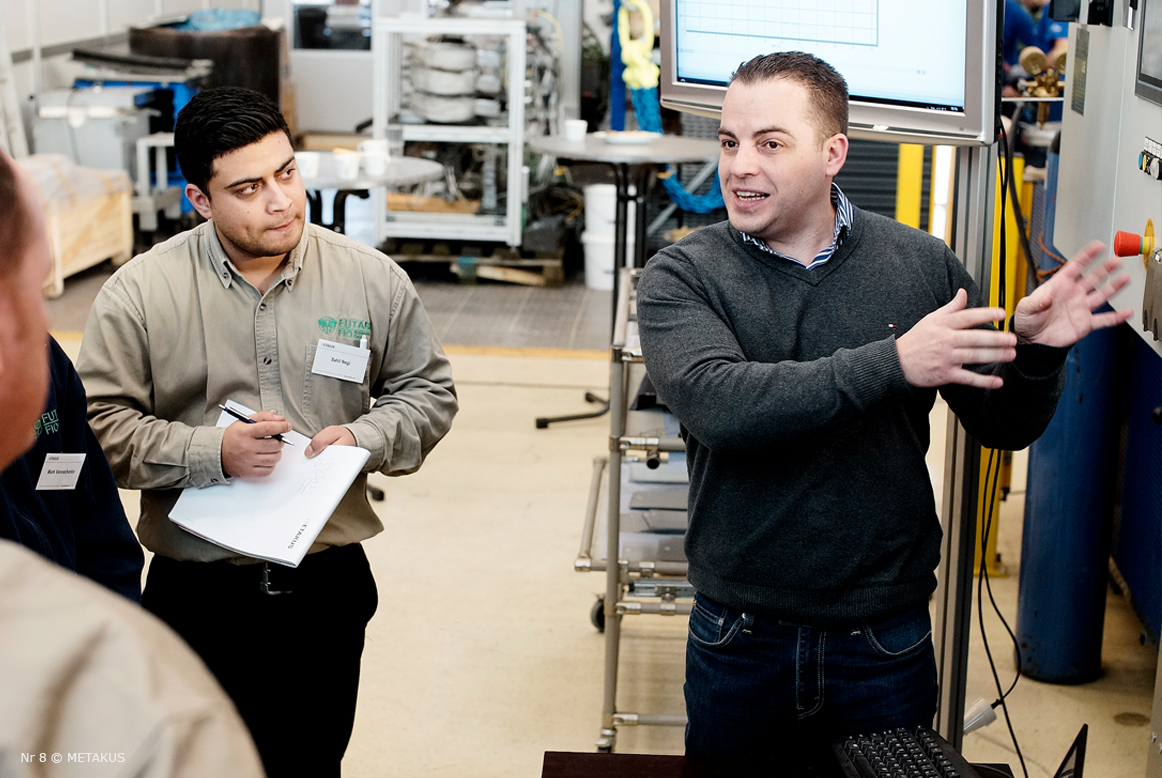